Corrocoat coatings are specified for applications as diverse as tank and vessel linings, pipeline coatings, concrete paints, structural steel protection, and refurbishment of pumps, valves, containers, filters, etc. ECR glass flake provides better qualities than standard glass flakes and in conjunction with highly modified resin systems provides a very low permeation, mechanically strong, tough, and abrasion-resistant coating with outstanding long-term performance.
Corrocoat glass flake coating material
Excellent adhesion strength, better than any other generic coating type.
●A high binder effect is brought about by resin due to high glass flake composition.
●High solids coatings – in many cases approaching 100% – have an extremely low VOC content.
Coating materials vary quite significantly; a coating that is filled with flaked glass offers superior protection thus, reduce the permeability of the coating system.
The material that offers the best all-around properties is corrosion-resistant glass. Because of this, most flake-filled coatings are formulated using glass flake.
Corrocoat products are formulated using micro flakes ECR glass that provides extremely impermeable and high bond strength.
Corrocoat Coating Material
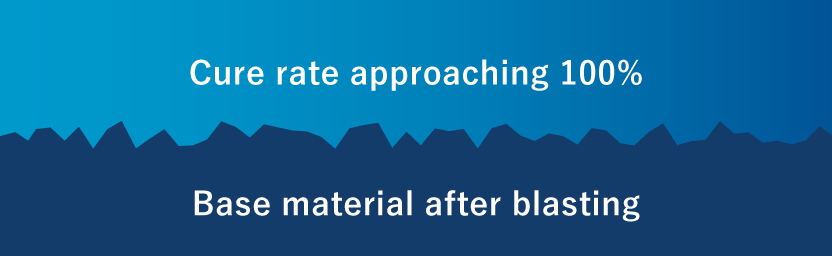
A low shrinkage rate during cure is obtained due to the flakes of glass preventing movement of the resin binder during the curing process
Generic Coating Material
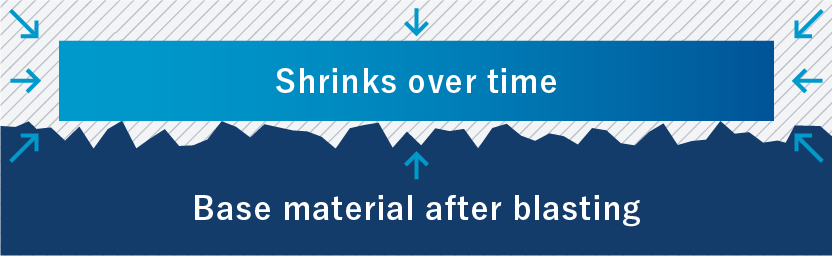
A general coating material has a large shrinkage rate at the time of curing, low resistance to undercutting .
Exellent Abrasion Resistance
Increase in abrasion resistance due to the high aspect ratio of the glass flake.
The resin beneath the glass flake is protected and once the surface resin has been removed, in order to further abrade the composite the glass flake has to be eroded away.
This results in an abrasion resistance much closer to that of the filler than that of the binder.
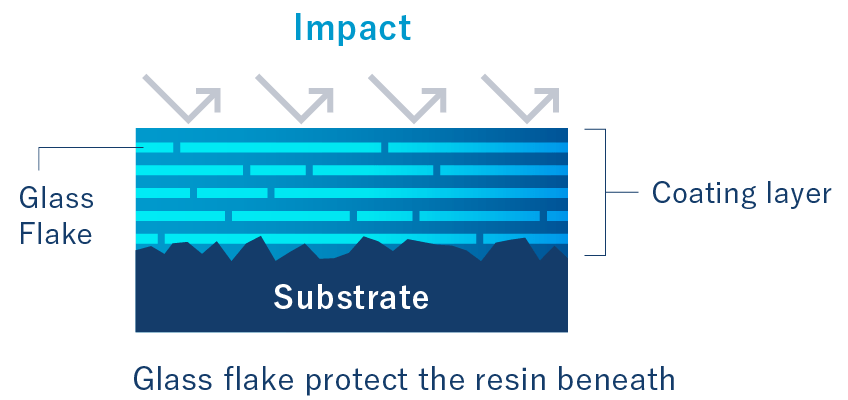
Coefficient of thermal expansion similar to low carbon steel
A similar coefficient of thermal expansion arises because of the compound expansion between the resin (with a higher rate than steel), and the glass with a lower expansion rate when blended in the correct proportions.
Machinable after curing
It has the same machinability as metal and can finish the construction surface with the required accuracy.
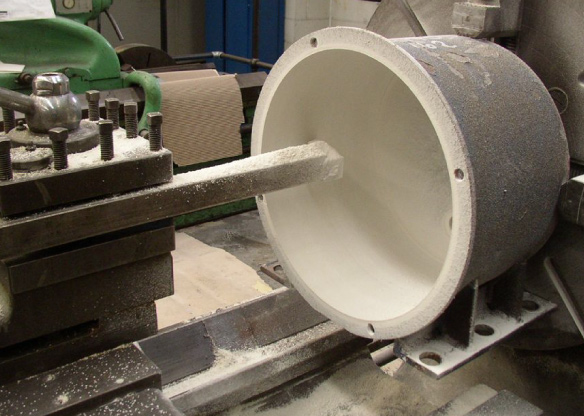
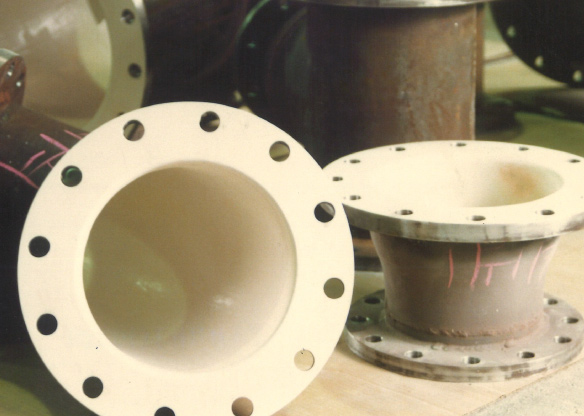
Corrocoat glassflake coatings
Corrocoat products are formulated with micro flakes ECR glass. The flake provides Improved permeation resistance, Isotropic mechanical reinforcement, and Improved heat and dimensional stability. The hardness of the glass offers mechanical reinforcement, as well as improvements to wear resistance.
Comparison of glass flakes
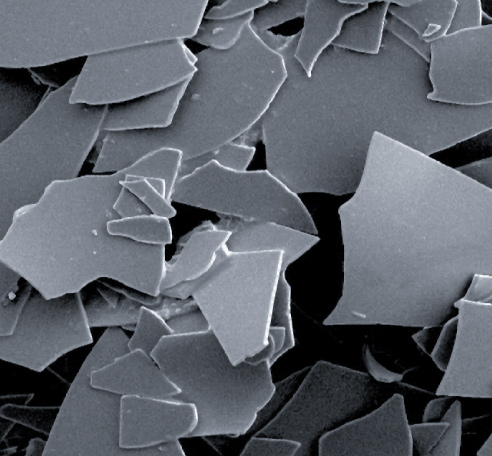
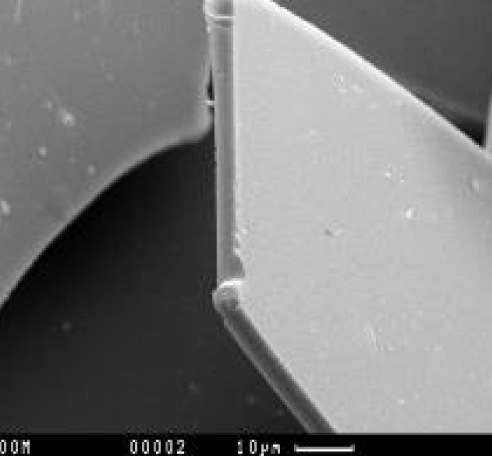
Corrocoat Coating Material
The glass flakes used by Corrocoat are ultrathin,
uniform,
have little variation, and do not contain impurities.
Generic Coating Material
The general purpose glass flakes are thick, not
uniform and contain impurities such as calcium
carbide.
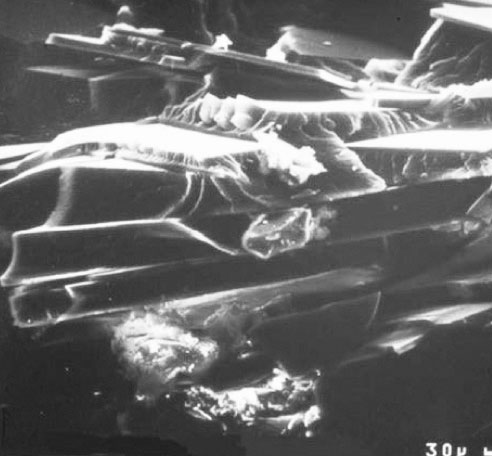
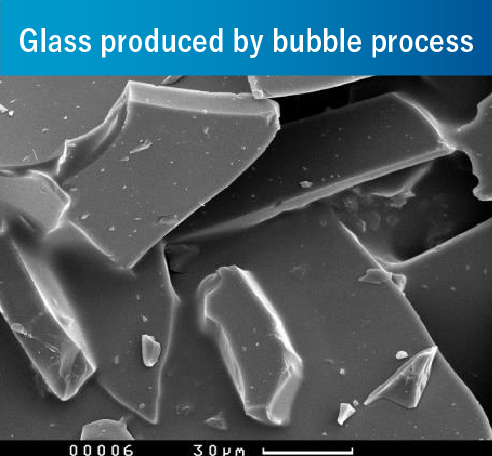
Coating material with low Vapour Transmission
The flaked glassfilled coating systems provide a long tortuous path through the binder in order that corrosive ions traveling through the permeable binder have to travel a much greater distance. The size of the flake, i.e. the diameter is what determines how far in a lateral direction corrosive ions have to travel, also the symmetry of the flakes.
[ Path Length for Moisture Vapour Transmission ]
Corrocoat Coating Material
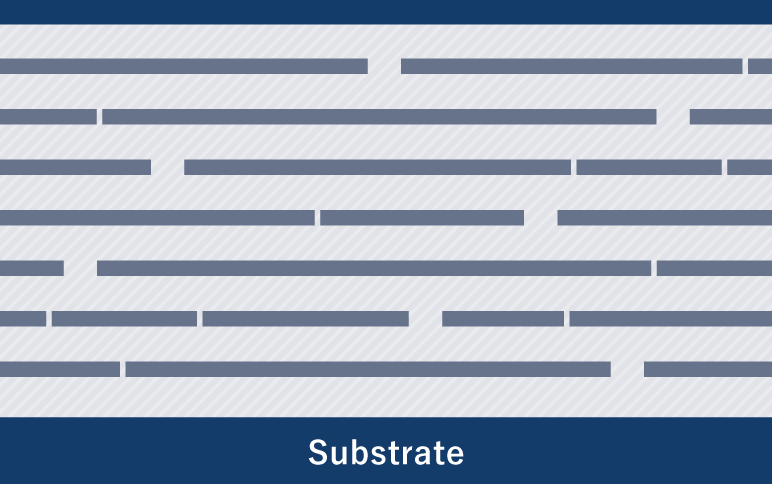
Generic Coating Material
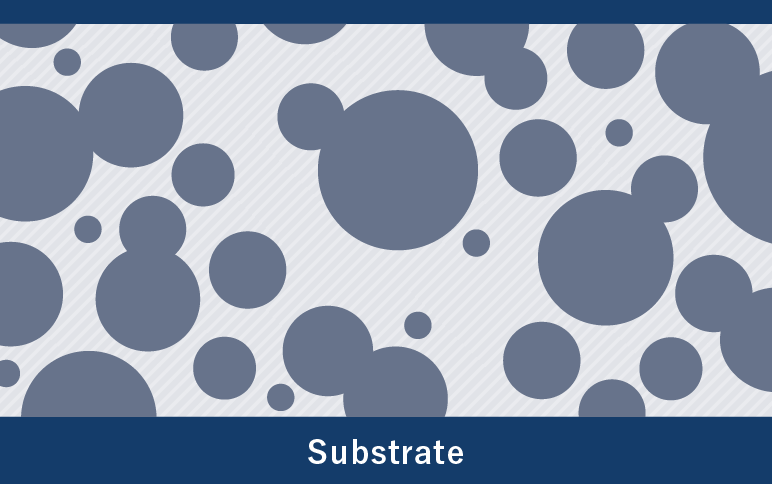
The tortuous path properties are approximately twenty times the path length of an unfilled binder. The higher the aspect ratio the greater the path length.
[ WATER VAPOUR TRANSMISSION ]
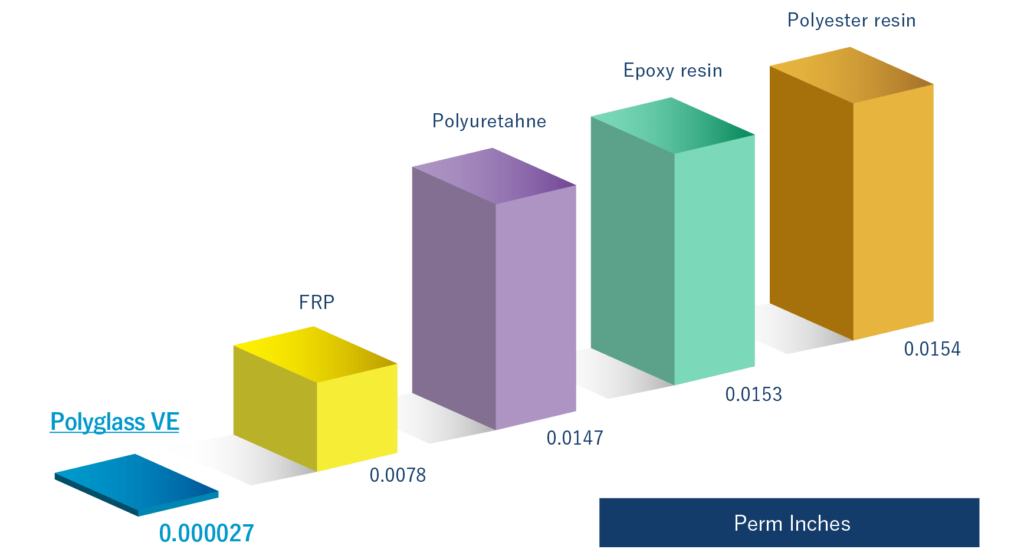
Compared to other coating materials, Corrocoat’s “Polyglass VE” has a vapor penetration rate of 0.000027, and “Coroglass 600 Series” has a vapor penetration rate of 0.000060.
Corrocoat products are the first choice.
Corrocoat products are perfect for withstanding harsh operating environments. Our unique high-performance composites and coatings not only fight against corrosion but also prolong the life of metals and machinery.
High performance coating systems. Polyglass VE series
Advantages of Polyglass VE series
- Low maintenance cost with lining to SS material than expensive SUS series steel material.
- Short delivery time due to single coat system
- Chemical resistance and high corrosion resistance for a wide range of pH values
Polyglass VE series for different types of applications.
- Polyglass VE: Airless Spray/Brush
- Polyglass VEF: Airless Spray/Brush
- Polyglass VEHA: Specializing in hand applications
- Polyglass VEPG: Specializing in pipe applications
Polyglass VE in corrosive environments
- VEF is suitable for many chemical environments within the full pH range, it has excellent resistance to demineralized water and good resistance to many solvents. It is also used in aggressive atmospheric or spillage conditions (bund areas) and potable water applications.
- Polyglass VE series can be used on a wide variety of substrates including Steel and Concrete, and has been used for protection in the Offshore, Oil and Petrochemical, Power Generation, Marine, Water/Sewerage and Process industries.
Physical property data (Polyglass VEF)
Specification | Polyglass VEF |
Specif gravity (gms/cc) | 1.19 |
Tensile strength (kg/c ㎡) | 272 |
Adhesive strength (kg/c ㎡) | 200 |
Hardenes Barcol | 45 |
Flexural strength (kg/cm2) | 166°×1.4kg |
Enlogation at Break(%) | 0.6 |
Abrasion resistance(mgm) | 216 |
Water vapor permeability (palm inch) | 0.0000267 |
Thermal coef. of linear expansion (1℃) | 19.7×10-6 |
Temperature limit (℃) immersed | 110 |
Temperature limit (℃) nonimmersed | 185 |
Thermal conductivity (W/mᵒK) | 0.398 |
Dielectric strength (kV/mm) | 18〜25 |
Recommended film thickness (mm) | 0.5〜3.0 |
High temperature and corrosion resistant. Corrothane XT
Advantages of Corrothane XT
- Low maintenance cost on existing equipment than changing to expensive material.
- A comprehensive solution that saves labor cost and time.
- Cold cured vinyl ester hybrid for coating steel and concrete where high temperatures and chemicals concentration are present.
Resistance for a wide range of pH values.
High performance of Corrothane XT
- For coating both steel and concrete surfaces, where good chemical and high temperature resistance are required, either for immersed or non-immersed service.
- Corrocoat XT is developed by Corrocoat to perform well in immersed conditions at temperatures up to 150oC and in non-immersed environments up to 260oC (these temperature values may vary, dependent upon environment).
- Corrothane XT is a urethane/vinyl ester polymer alloy with excellent resistance to chemical environments and high temperatures. Corrothane XT contains high performance ECR glass flakes.
Physical property data (Corrothane XT)
Specification | Corrothane XT |
Temperature limit (℃) immersed | 150 |
Temperature limit (℃) nonimmersed | 260 |
Tensile strength(㎏/cm2) | 175.69 |
Adhesive strength(㎏/cm2) | 546 |
Hardenes Barcol | 57 |
Flexural strength kg/cm2 | 170.0°×1.7 ㎏ |
Compressive strength(㎏/cm2) | 1267 |
Enlogation at Break(%) | 0.42 |
Abrasion resistance (Taber test mg) | 258( grinding H-18 ) |
Vapor permeability (perm inch) | 0.000061 |
Vapor permeability (g / ㎡h) | 0.00095 |
Click here for a list of Corrocoat coating material products