Corrosion resistant coating.
“Benefits”
Corrosion resistant protection.
Repair and refurbishment
Where repairs to corrosion damaged equipment are needed to be carried out first, corrosion resistance coating takes place as a base coat.
【 Corrosion resistant coating 】
After disassembling.
Worn and corroded part
inside of the casing.
Enlarged image of the damaged area.
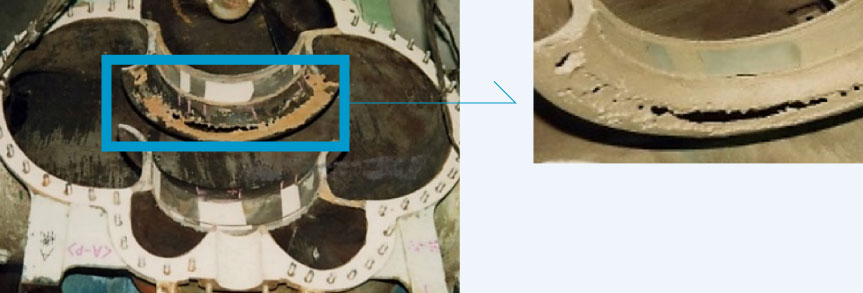
After coating and refurbish
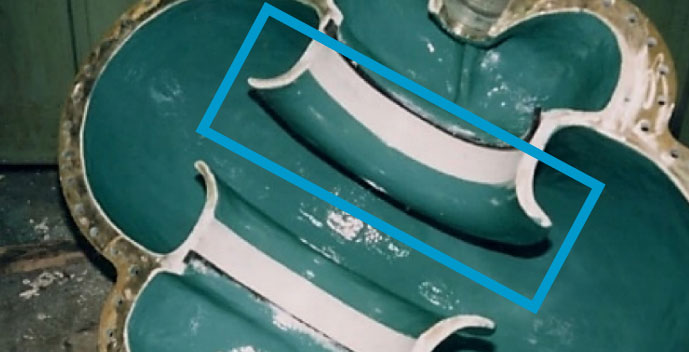
Before coating: Worn and corroded impeller
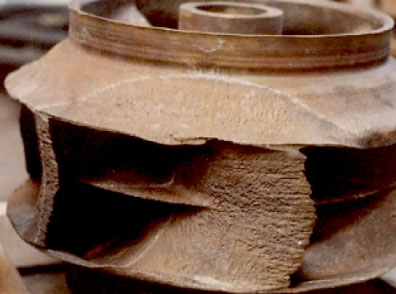
After coating: Profile regeneration

Before coating
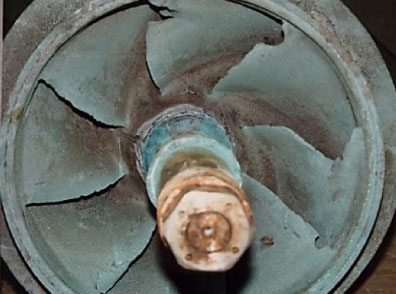
After coating
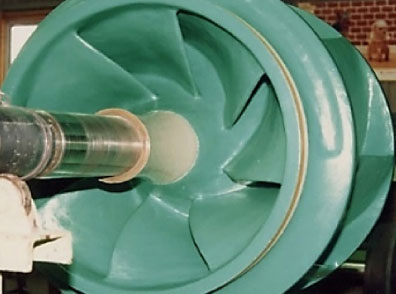
Significant improvements in efficiency
“Fluiglide coating is effective friction-reducing”
Corrosion resistant protection
Repair and refurbishment
The “Fluiglide” coating with a significantly lower roughness amplitude than cast iron offers a smooth path for fluid flow, reducing the frictional losses and directly contributing to the enhancement of efficiency.
(Comparison roughness of coating surface)

Cast iron: Ra 18.8 μm

Mild rusted Steel: Ra 5.0 μm

(*) Fluiglide: Ra 0.04 μm
(*) Tests carried out in Japan
Another characteristic in improving efficiency is the hydrophobic nature of the surface.
When the attractive force between the substrate and the water molecules exceeds the cohesive forces in the liquid, the water or other media will spread across the surface until a state of equilibrium is reached between the two.
Therefore, where the surface energy is high, low contact angles will be achieved, and where the surface energy of attraction is low, the high contact angles will result in larger gradients in velocity between the mainstream flow and the boundary layer.
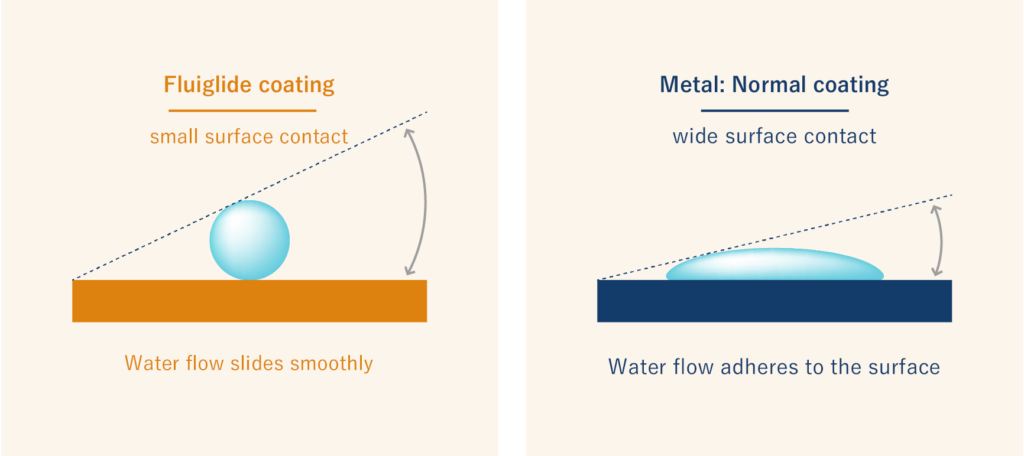
As shown in the figure above, in the case of metal or general-purpose coating, the liquid spreads to the surface and the contact area of the liquid is large, which is one of the causes of lowering the pump efficiency and leads to an increase in power.
Fluiglide coating flows with a small contact area of the liquid with the object, resulting in improved pump efficiency.
Pump Servicing and Monitoring
Corrosion resistant protection
Repair and refurbishment
Through rigorous analysis of our diagnostic and monitoring services, we can identify significant long-term cost-saving opportunities for pump operation.
Corrocoat offers a comprehensive service for measuring pump efficiency thereby identifying the optimum moment for pump refurbishment or replacement.
Our service combines the advantage of the Thermodynamic Technique Analysis and The Proactive Maintenance Service.
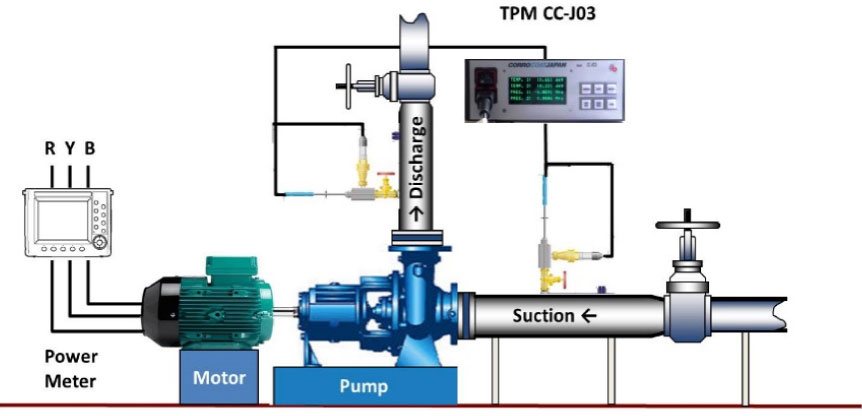
POINT
- Pump Performance Testing.
- System & energy Analysis.
- Project Management & Proactive Maintenance Service.
- Fluiglide Coating System & Pump Repair and servicing.
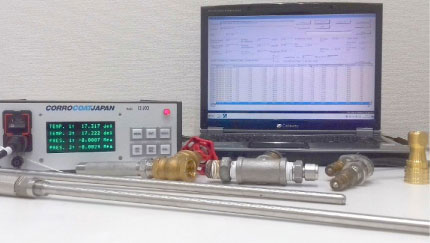
[ Characteristics of pump performance measurement / monitoring system ]
- The system uses the Thermodynamic Method (ISO 5198 “Centrifugal, mixed flow and axial pumps – Code for hydraulic performance test – Precision class”).
- This method requires measuring only two parameters (temperature & pressure) to compute the pump efficiency.
- It is easy and inexpensive to install with a minimum of disruption to operations. Real-time pressure and temperature data are shown in the pane.
- The TPM Software computes the pump efficiency, flow rate, and total head.
- The system can measure the changes in efficiency to provide an economic justification of pump refurbishment or replacement.
[ Pump performance is displayed quickly for easy interpretation ]
The standard parameters of Head, Efficiency, and Power are plotted together against flow-rate on a stacked axis char.
These parameters are compared before and after coat to witness the increments in pump efficiency and energy saving.
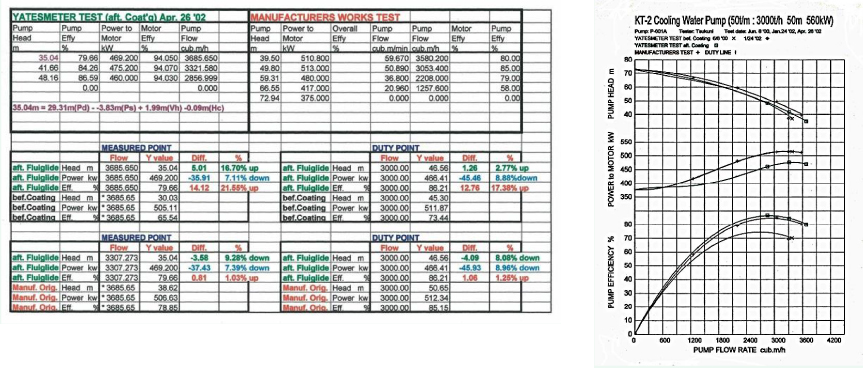