Project | Water pump Energy saving |
---|---|
Target | Power saving by Fluiglide coating on cooling tower pump |
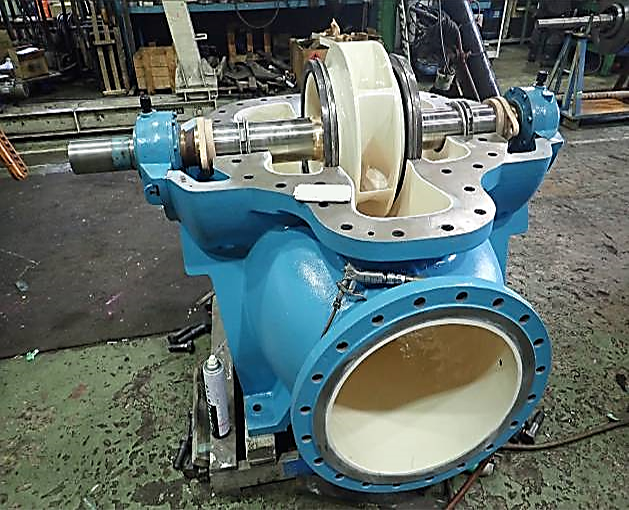
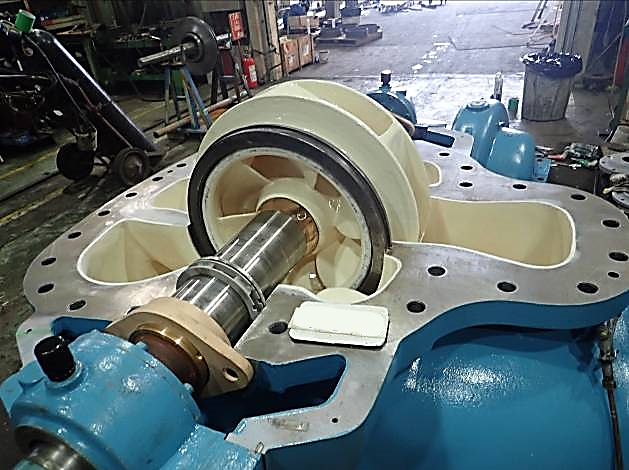
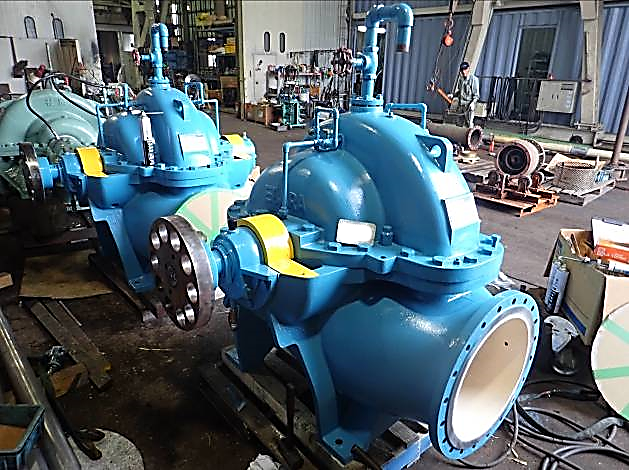
Photo description
Coating completion and assembly process
Coating completion and assembly process
After completion of assembly
Customers and industries
Chemical Industry
Target equipment
Cooling tower pump
Target Item
Φ500 × Φ350 Double suction pump
Coating period
October 2019
Scope of work
■ Monitoring of pump performance prior to coating application to estimate savings in energy consumption and increases in pump efficiency.
Determining information to decide the anticorrosive protection system to apply.
■ Application of the fluiglide coating system and general maintenance of the pump, including the manufacture of defective parts.
Determining information to decide the anticorrosive protection system to apply.
■ Application of the fluiglide coating system and general maintenance of the pump, including the manufacture of defective parts.
Materials used
Fluiglide, Corroglass 200
Coating process
1. Pick-up and delivery
2. Pump maintenance, disassembly and assembly
3. Replacement of worn parts
4. Manufacture and replacement of defective parts
5. Application of Fluigide coating on the inner surface (anti-corrosion treatment on the outer surface)
6. Pump Performance monitoring after installation (on site)
2. Pump maintenance, disassembly and assembly
3. Replacement of worn parts
4. Manufacture and replacement of defective parts
5. Application of Fluigide coating on the inner surface (anti-corrosion treatment on the outer surface)
6. Pump Performance monitoring after installation (on site)
Merits of this application
We plan to service save energy coating by targeting pumps that have a long operating time per year and have a relatively large power load.
We carried out the pump performance monitoring that is normally performed before and after coating application.
Pump maintenance is also performed at the same time, including the manufacturing of some parts.
We carried out the pump performance monitoring that is normally performed before and after coating application.
Pump maintenance is also performed at the same time, including the manufacturing of some parts.
Corrocoat Japan credentials etc
After delivery, performance measurement is carried out to verify the pump performance and energy saving merit after coating.
Although it is a comparison with the new product, we confirmed the energy saving merit of 35.16㎾ / h, 9.2%, that’s 281,280 kWh/year.
Although it is a comparison with the new product, we confirmed the energy saving merit of 35.16㎾ / h, 9.2%, that’s 281,280 kWh/year.